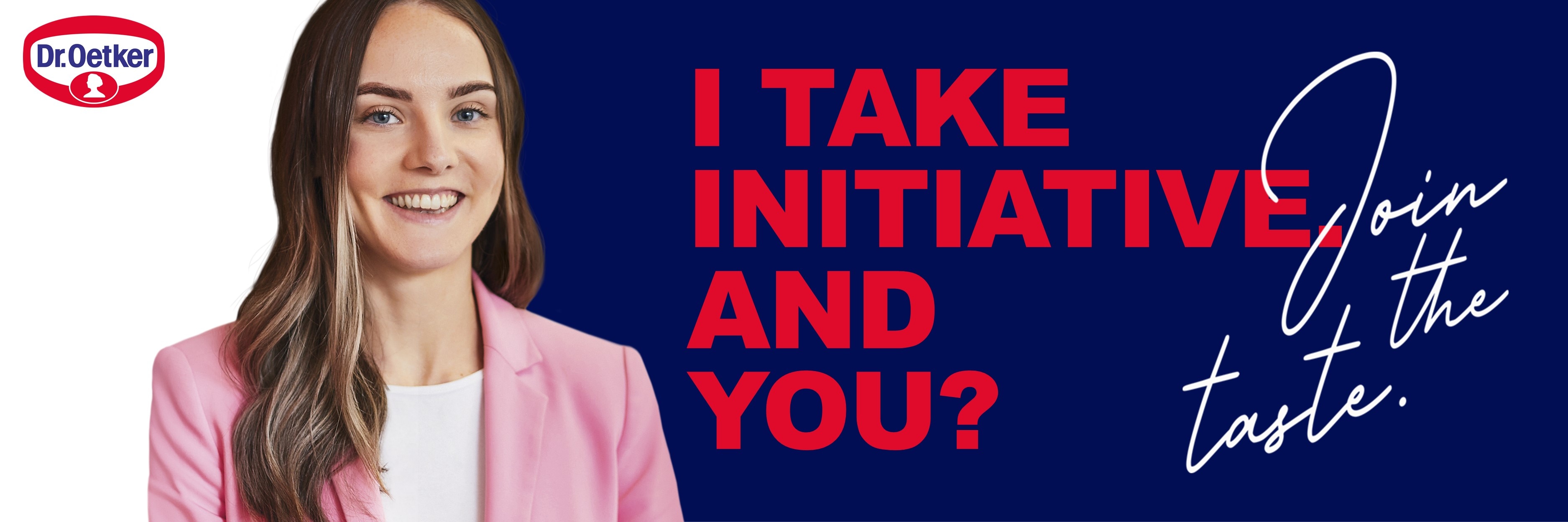
Reliability Manager
Maintenance | Leyland | Start date: 01/08/2025 | Full Time | Permanent
PURPOSE OF ROLE:
As the Reliability Manager, you will be responsible for ensuring the reliability and performance of all production assets in a high-volume manufacturing environment. Reporting directly to the Head of Maintenance, your role will focus on maximizing asset reliability, reducing downtime, and optimizing maintenance operations. Additionally, you will develop strategies for preventive maintenance, asset performance monitoring, and root cause analysis of equipment failures. By managing resources effectively and collaborating with cross-functional teams, you will ensure the seamless operation of our production lines while improving overall equipment efficiency.
KEY RESPONSIBILITIES:
Asset Reliability Management
• Implement asset reliability strategies to ensure the optimal performance of all production equipment, including ovens, packaging machines, and refrigeration systems.
• Conduct regular reliability assessments on critical production assets to monitor condition and performance trends, identifying areas of potential improvement.
• Develop and maintain equipment reliability standards to guide all maintenance activities and ensure consistent performance across the facility.
• Establish and track key reliability metrics, such as equipment downtime, number of breakdowns, and maintenance costs, to evaluate asset performance and highlight areas needing attention.
• Generate actionable reports on asset health and reliability, communicating findings to senior management and other key stakeholders.
• Identify and address obsolete or surplus inventory, proposing solutions to optimize inventory holdings and reduce waste or unnecessary costs.
Root Cause Analysis & Continuous Improvement
• Lead root cause analysis (RCA) for recurring equipment failures, ensuring that effective corrective actions are taken to prevent future issues.
• Utilize data-driven methods to analyse equipment failures, downtime events, and maintenance data to identify recurring trends and underlying causes.
• Implement corrective actions derived from RCA to eliminate root causes, ensuring that the improvements are sustainable over the long term.
• Drive the development and execution of reliability-centred maintenance (RCM) strategies, focusing on improving asset life cycle management and reducing unplanned downtime.
• Encourage a continuous improvement mindset across the maintenance and production teams, fostering a culture of proactive asset management and operational excellence.
Collaboration & Cross-Functional Support
• Collaborate with production, maintenance, procurement, and inventory teams to prioritize maintenance tasks and ensure resource availability, balancing operational needs with reliability goals.
• Provide technical expertise and support to maintenance teams in troubleshooting and resolving complex equipment issues, offering guidance on equipment repairs and process optimization.
• Act as a liaison between departments, ensuring that maintenance activities are aligned with overall company objectives, including production goals and cost-efficiency targets.
• Champion best practices for maintenance activities across teams, ensuring that standardized procedures are followed and improving overall team performance.
We look forward to your online application. Just click the "Apply now" button, and you're good to go. Still have questions? Then please feel free to reach out to us directly.
Dr. Oetker is an equal opportunities employer. We continuously work to shape and live in a corporate culture where everyone feels welcome. At Dr. Oetker, your personality and qualifications are what count. Not gender, nationality, ethnic or social background, religion, disability, age or sexual orientation, and identity.
Dr. Oetker (UK) Limited
LeylandRecruitment@oetker.co.uk